Hydroponics: Progress Report 8-Mar-2023
Here’s what’s been done since the last report
- Lights arrived, and the ones for Tower 1 were installed
- Plants were migrated from germination tank to Tower 1
- The plant nutrient solution management process was established
- The plant light-level management process was established
Here’s what’s coming up next
- Begin formal testing. Set a baseline of how the plants were at the outset, and start measuring how they progress over time
- Get good at operations. Some aspects of this – especially managing the nutrient solution – I’m very much the novice at. I need some just-in-time learning
- Determine what the key operational indicators (metrics) are, and find an easy way to collect and evaluate that information
- Fix problems. We’ve got issues, and they need to be gradually addressed
- Germinate some more plants, pronto! We’ve got 8 open slots right now
- Decide when to begin fabricating Tower 2. At what point am I confident enough in the current design to invest the time and material to extend it another tower?
Issues
We’ve got some known issues:
- The open tower sockets are admitting light into the interior of the tower cylinder. I want that interior to be dark, dark, dark so no algae can grow there. Need a patch.
- The trickle-down rate of nutrient solution seemed to change after I installed the plants into the tower. Why is that? Changing flow rate is not a good thing; I want that to be stable, because that’s a key input to the “how often to cycle nutrients” calculation that the robot is making
- The white plastic I used to print the tower components admits too much light. I need to choose a (much) darker color plastic for the next tower, and I may need to paint or otherwise darken Tower 1
- The drain collector funnel at the bottom of the tower has an exit opening of about 1/2 inch. That may need to be widened, and for that, I’ll have to design (not just print) a replacement part. That’s going to be a significant learning curve for me
- It seems possible that roots growing downward from the bottom tier of plant sockets on Tower 1 may get long enough to clog the exit port on the collector funnel. I may need to implement some evasive maneuvers to avoid that problem
The Pix
Here are a few more pix to give you a better feel for how this thing is coming together.
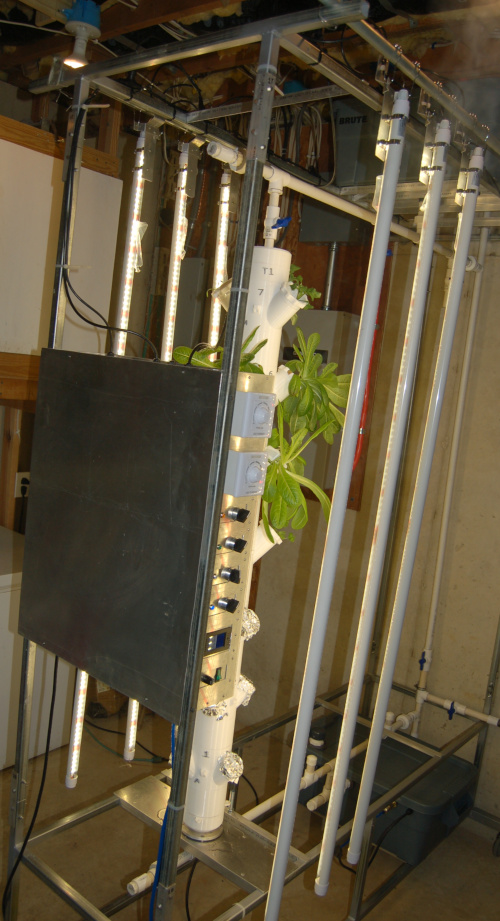
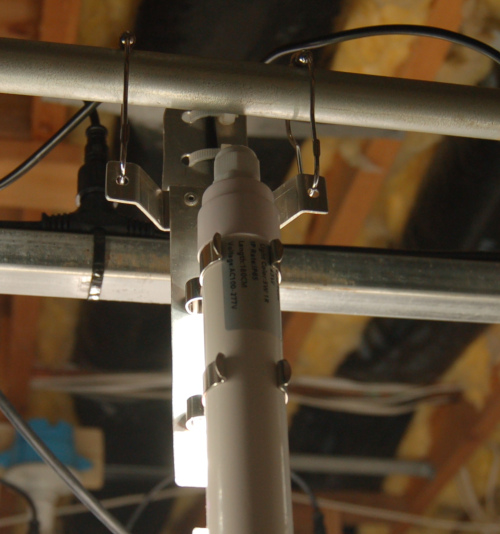
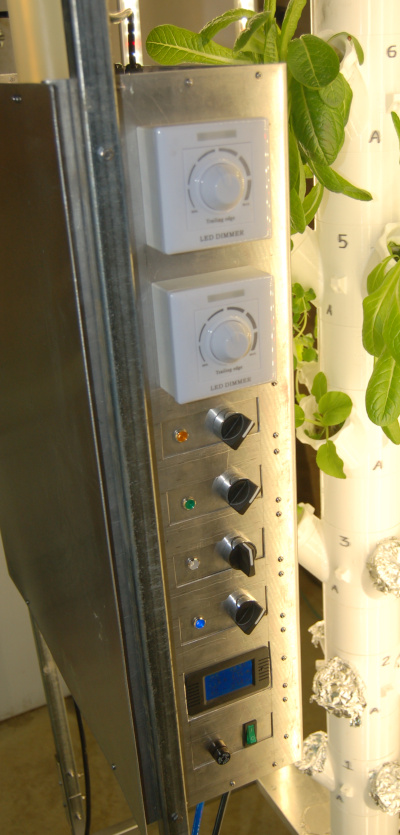
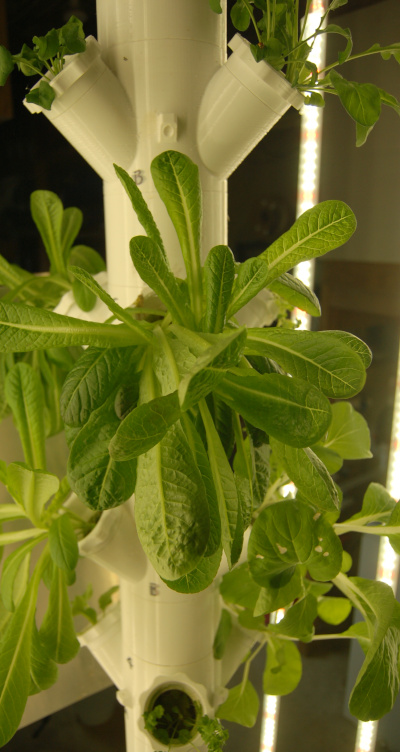
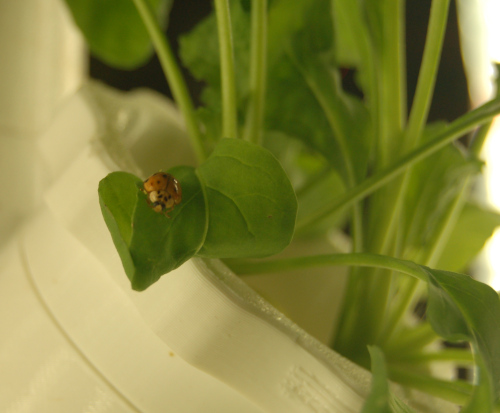
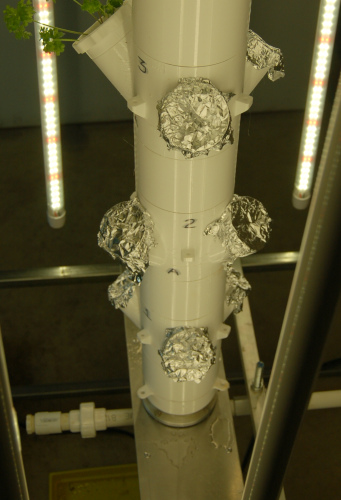
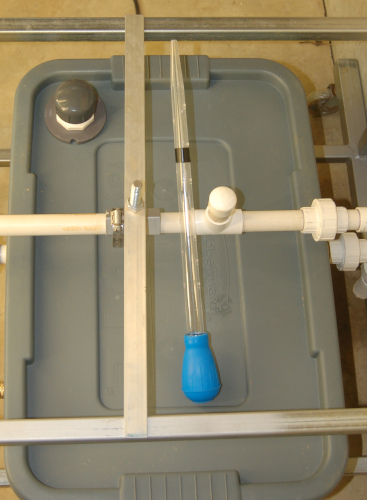
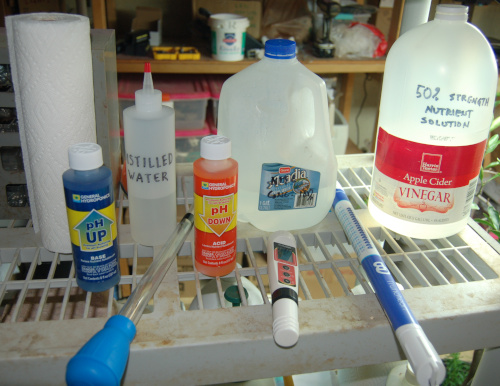
Share this content:
4 comments